The procedure of CNC machining requires making use of a computer system to control device devices for an extra consistent and reputable output. This technology converts CAD (computer-aided design) designs straight right into machine-readable code, which guides the machining process. The result is that makers can generate get rid of consistent high quality and accuracy, lowering waste and the risk of error in production. In the situation of copper, which can be rather tough to machine because of its thermal conductivity, high ductility, and propensity to work-harden, CNC technology offers the adaptability required to resolve these problems effectively. Specialized methods and devices are often employed to enhance the machining process, which can consist of utilizing reducing devices coated with difficult products to minimize wear and improve performance when functioning with soft steels like copper.
Discover copper cnc machining exactly how copper CNC machining merges sophisticated innovation with sustainable methods to create elaborate, high-precision elements, driving advancement across markets such as electronic devices, auto, and aerospace.
Among the main benefits of CNC machining copper is the ability to create complicated shapes that traditional machining methods may not suit. The repeatability of the CNC machining procedure makes sure that mass manufacturing of copper components preserves uniformity, thus meeting stringent industry criteria.
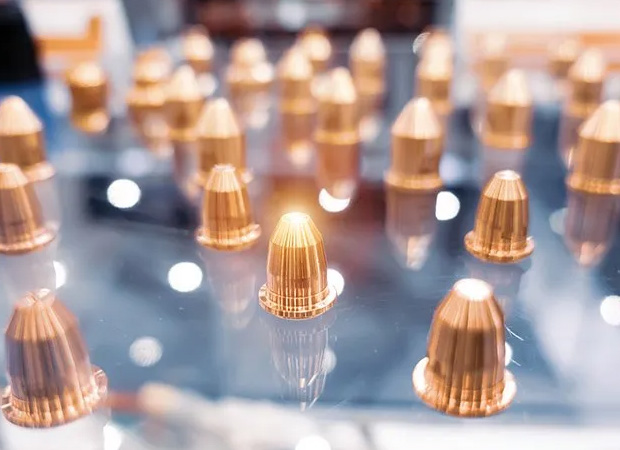
Temperature management plays a crucial function in the CNC machining of copper due to its ability to perform heat swiftly. High-speed machining can lead to significant warm generation, which may negatively influence the homes of the copper and exacerbate device wear.
The sustainability facet of CNC machining copper is not to be overlooked. CNC machining, combined with lasting techniques, can decrease waste by enabling makers to utilize scrap copper from other processes.
In enhancement to sustainability, cost-effectiveness is one more important variable for suppliers picking CNC machining for copper parts. CNC machining supplies a decrease in labor prices due to its automatic nature and reduces the requirement for substantial hands-on treatment. Furthermore, for little to medium batch manufacturing runs, CNC machining can verify extra affordable contrasted to typical machining procedures, as it permits for smooth changes and layout changes without comprehensive retooling.
Furthermore, as innovation progresses, the performances within CNC systems are broadening, additionally improving the abilities of copper machining. The assimilation of simulation software program permits producers to forecast potential concerns prior to the machining procedure begins. These simulations enable far better preparation of tool courses and clarify exactly how the copper material will certainly respond throughout the machining process. By identifying and resolving possible difficulties in advancement, companies can minimize downtime and rise efficiency, creating a smoother functional circulation.
Education and competence in CNC machining are vital for realizing the complete possibility of copper processes. Skilled machinists must be skilled in translating design requirements, choosing the appropriate devices, and changing machining parameters to mitigate issues related to copper's distinct machining characteristics. In addition, the improvement of additive manufacturing modern technologies, such as 3D printing, has created brand-new paradigms in the handling of copper. Hybrid machining, which integrates traditional CNC machining approaches with additive manufacturing, is becoming a practical method for creating intricate copper parts, blending the toughness of both innovations and possibly reinventing how makers approach copper manufacturing.
In the realm of research study and advancement, CNC machining is assisting the exploration of new copper alloys to improve efficiency better. As global industries work towards better power efficiency, copper's role as a conductor in electronic circuits will continue to be extremely important, driving need for advanced machining services.
The aerospace and vehicle sectors are additionally eager adopters of copper CNC machining, especially where lightweight elements are of crucial significance. As the shift toward electric and hybrid cars continues, the demand for high-performance copper parts will likely rise, therefore thrusting the requirement for sophisticated CNC machining methods that make sure effectiveness and high quality in production.
As CNC machining technology continues to develop, it enables more automation, where essential processes such as tool changes, evaluations, and maintenance can be programmed right into the manufacturing cycle. This development indicates that makers will be able to attain greater efficiency levels, shorter lead times, and greater flexibility in accommodating custom demands or variants in style. Because of this, companies that take part in CNC machining operations are much better matched to pivot in feedback to the changes in consumer and market demands, fostering development in a progressively competitive landscape.
Discover countersink size chart exactly how copper CNC machining merges innovative modern technology with lasting techniques to create elaborate, high-precision components, driving innovation throughout markets like electronics, auto, and aerospace.
The worldwide market for CNC machining of copper is witnessing substantial development, influenced by variables such as the surge of wise technologies, electrical automobiles, and continuous efforts to boost power efficiency throughout numerous applications. It shows a converging fad where services embrace electronic production practices, aiding form the future of manufacturing. Developing collaborations with providers, modern technology suppliers, and academia can enhance accessibility to the current innovations and expertise within the field, cultivating a collective environment that drives forward-thinking campaigns. In this development, training and skill advancement continue to be vital; investing in labor force education on CNC machining strategies, developments, and product sciences will certainly empower makers to stay in advance of the curve.
As markets progress and the borders of technology expand, accepting CNC machining's capacity will certainly be key to recognizing unmatched development and innovation in the usage of copper products. The harmony of copper's product buildings with advanced CNC machining methods advertises a brand-new age in which sustainability, effectiveness, and accuracy work together to produce cutting edge parts that will define the future of production and beyond.